In chemical plants, explosion-proof motors are a crucial component of operational safety. This article explains the significance of explosion-proof motor ratings in these environments and how they help prevent catastrophic incidents. Additionally, we explore the role of geonets in enhancing the motor’s durability.
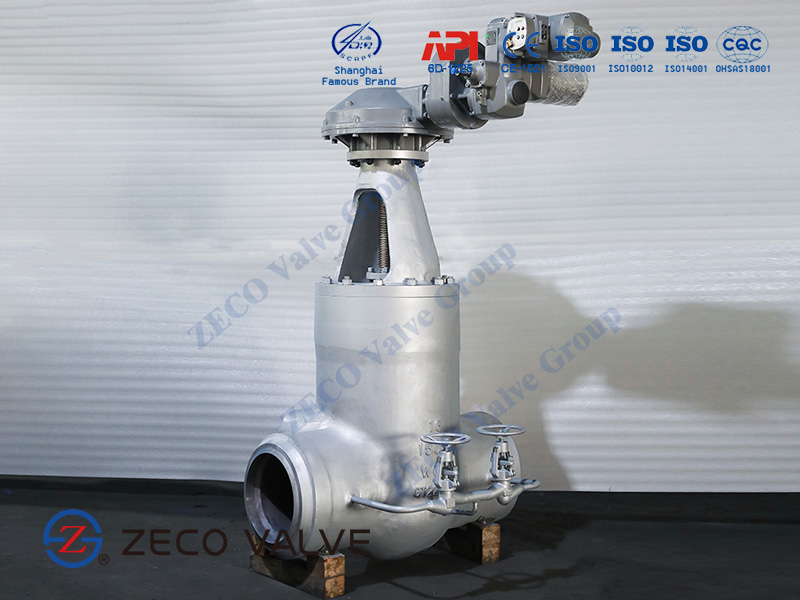
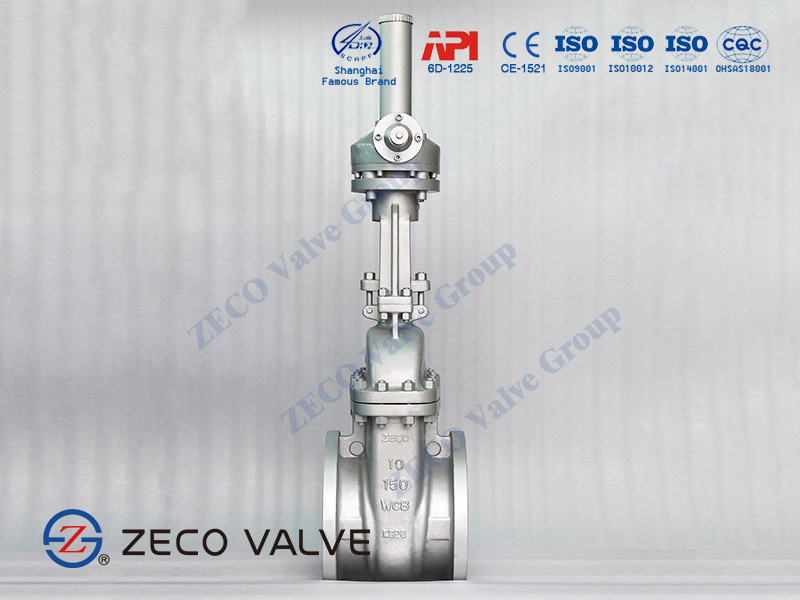
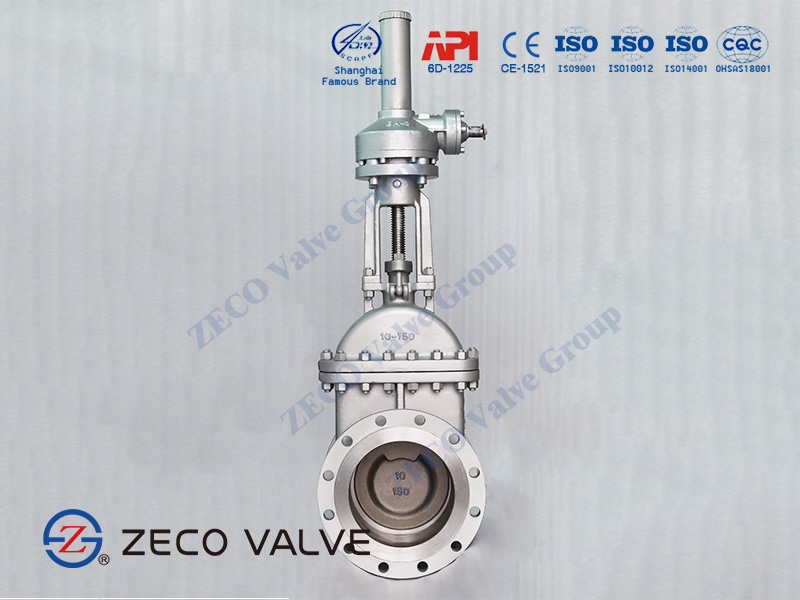
Why Chemical Plants Require Explosion Proof Motor Ratings
Chemical plants often deal with volatile substances that can easily ignite. Explosion proof motor ratings ensure that the motors used in these environments are designed to contain internal explosions and prevent sparks or flames from escaping. This is essential for maintaining a safe environment where hazardous chemicals are processed.
Key Features of Explosion Proof Motor Ratings for Chemical Plants
Explosion proof motor ratings are determined by factors such as:
- Temperature Class: The motor’s maximum allowable surface temperature, ensuring it doesn’t ignite surrounding chemicals.
- Group Classification: Categorizing motors based on the types of gases present, such as acetylene, hydrogen, or methane.
- Zone Classification: Specifying the level of risk in the environment (Zones 0, 1, or 2).
These ratings determine the motor’s ability to safely function in a chemical plant’s explosive atmosphere.
In harsh environments like chemical plants, explosion-proof motors need added strength. Geonets—strong, durable materials—are often incorporated into motor construction to improve their resistance to wear and external pressures. These geosynthetics enhance the motor’s ability to withstand the harsh conditions common in chemical processing.
Explosion proof motor ratings are essential for ensuring safety in chemical plants. By understanding these ratings and integrating materials like geonets into motor designs, companies can safeguard their equipment and personnel from explosion risks.