gate valve symbol in isometric drawing
2 inch gate valve dimensions
rubber seat flanged gate valve
gate valve socketweld
gate valve box cover
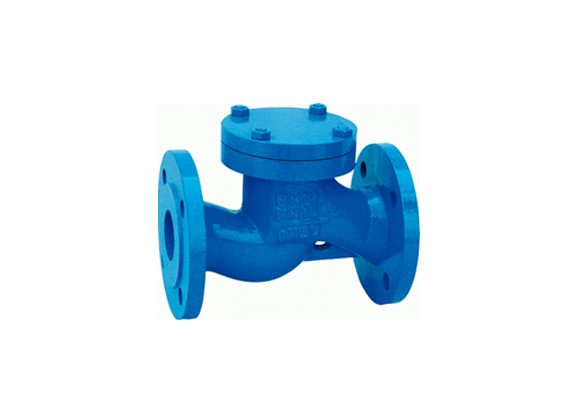
Flange Ball Valve is a control component in the piping flow system used to cut off and distribute the direction of the medium flowing in the pipeline. In operation, a rotation of 90 degrees with a small torque is sufficient to close the valve tightly. Flanged ball valves are made of metals such as carbon steel, stainless steel or brass, making them robust and strong.

■ If the valve is used within the rated range, following design parameters, its operational life can be maximized
■ Refer to the general assembly drawing of the valve for understanding the internal construction
■ Keeping the flange ball valve in throttled position is not the best practice as this may cause damage and seat life may reduce.
■ Every material capable of solidifying, crystallizing, or polymerizing should not be permitted to remain in the ball cavity, because this may adversely affect the efficiency and reduce the valve life.
The quarter-turn rotation of the flange end ball valve is accomplished using a Lever / Gear unit / Hydraulic / Pneumatic or Electric actuator.
Gear Unit
Gear units provided on valves helps in easier operation. Typically, the clockwise operation is for closure and the anti-clockwise opening of the valve. The position of the valve can be shown using the location indicator given on the side of the gear panel.
Electric Actuator
It will give a multi-turn output and is installed on the gear unit or directly installed on the valve. The actuator powers the gear assembly, which in turn will rotate the shaft. Electrically actuated valves are fitted with a declutching system for the manual control of the valve. Actuator configurations are performed at the plant and usually adjustment or reset at the site is not advised
Note: Forcing the handwheel, the Chain wheel or nut against the stops will not provide a tighter shutoff of the valve and may damage the gear unit.
Pneumatic / Hydraulic Actuator
Generally, the pneumatic / hydraulic actuators are mounted directly to the valve without a gear assembly. It is advised that the guidelines must be strictly followed as per the actuator manual.

Handling & Storage
Handling
■ Before moving the valve, it must be properly supported and secured, to prevent possible damage to valve, property, or harm to personnel.
■ During transportation do not drag the valve on the ground. Maintain a minimum height from the ground while moving the valve.
■ Do not slung the valve around the valve port for transportation.
■ The crane wire must not be slung around the actuator/gear unit to avoid any load acting on it. While handling the valve, ensure that no external load acts on the actuator/gear unit.
■ Do not handle the valves with the handwheel keyed/fixed to the gear unit. Dismantle the handwheel before handling and transporting the valve.
Storage
■ The valves must be kept in a protected environment clear of dust and humidity and area should be well ventilated.
■ Please ensure that the end protectors are in position until the valve is placed, as dry pollutants such as dust, sand, grit, etc. can scrape metal seating surfaces and soft pieces, resulting in leakage during service.
■ The valve shall also be kept at a temperature greater than the temperature of the dew point at the storage location to prevent the accumulation of water droplets on the valve sheet.
■ Directly keeping the valve on the floor is strictly prohibited. Valve shall be placed on a wooden pallet such that it is at a minimum height from the floor.
■ Take special care for not damaging the extended portion of the adaptor, gear unit/ actuator while storage.
■ Application tar, non-compatible grease, or any other material inside the valve is not permitted, as it could impair the performance of the valve.
■ These valves must be dispatched in a fully open position, to protect the sphere surface and soft valve seats and it is recommended that they are left in this position.
■ A nontoxic “Manganese Phosphate” coating is used for the Carbon steel valves. This slows down the formation of rust during storage.
■ With their natural finish, Stainless Steel valves may not require additional protection once installed.
Instructions for Usage, Installation and Maintenance of Flange Ball Valve
Instructions for Usage of Flange Ball Valve
■ The assembly and disassembly of flange end ball valves can only be carried out after confirming that the upstream and downstream pipes have been relieved of pressure.
■ Non-metal parts should not be soaked for a long time in the cleaning agent and should be taken out immediately after cleaning.

■ The bolts on the flange must be tightened symmetrically, gradually, and evenly while assembling.
■ The cleaning agent used a flange ball valve that should be compatible with the rubber parts, plastic parts, metal parts, and working medium (such as gas). Use gasoline as a cleaning agent for metal parts when the working medium is fuel gas. The cleaning of non-metal parts can be done with pure water or alcohol.
■ Every part of the flange ball valve can be cleaned by dipping it into cleaning solutions even if the parts have degraded. Non-metallic parts can be scrubbed with a clean and fine silk cloth impregnated with a cleaning agent (to prevent fibers from falling off and adhering to the parts). Remove grease, dirt, glue, dust, etc. adhering to the wall while cleaning.
■ Take special care of non-metallic parts while disassembling and reassembling the flange ball valve to prevent damage to the sealing surface of the parts. Use special tools for removing the O-ring.
■ Wipe out the cleaning agent from the parts before assembling the valve with a silk cloth to make it dry & to remove all dust. Do not soak the parts in cleaning agents for a long period, it may get rusted.
■ New parts also need to be cleaned before assembly.
■ Lubricate parts with grease. Use a grease that is compatible with flange ball valve metal materials, rubber parts, plastic parts, and working media. For example: Use special grease 221 when the working medium is gas. Coated on the surface of the seal member mounting groove of a thin layer of grease, rubber seal member coated on a thin layer of grease coated stem seal surface and the friction surface of a thin layer of grease.
■ Special care should be taken during assembly to ensure metal debris, fibers, grease (except those specified for use), dust, and other foreign impurities do not contaminate or adhere/stay on the surface of the parts or enter the inner cavity of the valve.
Installation of Flange Ball Valve
■ Preparations before installation
1. The front and rear pipes should be coaxial and the sealing surfaces of the two flanges should be parallel. The pipeline should either be able to bear the weight of the Flange end ball valve or the pipeline must be equipped with proper support.
2. Purge the pipelines before and after the valve to remove oil, welding slag, and all other impurities present in the pipeline.
3. Check the sign of the flange ball valve and ensure it is fully intact. Check that the valve is working properly by opening and closing the valve several times.
4. Remove the protective parts of the flange ball valve at both ends of the connecting flanges.
5. Check the valve hole to remove and clean any possible dirt. Even small foreign particles between the valve seat and the ball may damage the sealing surface of the valve seat.
■ Flange Ball Valve Installation
1. Install the flange ball valve on the pipeline as required. Either end of the flange ball valve can be installed on the upstream end.
2. The flange end ball valve driven by a handle can be installed at any position on the pipeline. However, a flange ball valve driven by a gearbox or have a pneumatic drive should be installed upright, i.e., installed on a horizontal pipeline, and the driving device should be above the pipeline.
3. Install a gasket between the valve flange and the pipeline flange according to the pipeline design requirements.
4. The bolts on the flange should be tightened symmetrically, successively, and evenly.
5. Connect the pneumatic pipeline at last in case of a pneumatically driven flange end ball valve.
■ Inspection after installation
1. Operate the valve with a driving mechanism to open and close the flange ball valve several times. The operation should be flexible and without stagnation, confirming that the valve is working properly.
2. Check that the flange joint between the pipeline and the flange ball valve is sealing properly according to the design requirements of the pipeline.
Maintenance & Repair of Flange Ball Valve
Please follow all the handling instructions given at the start of this document for Maintenance & Repair of Flange Ball Valve.
Precautions for Repair and Maintenance
In addition to the normal working conditions, maintaining a harmonious temperature/pressure ratio, and reasonable corrosion data will ensure that the flange ball valve has a longer service life and maintenance-free period. Following precautions should be taken while carrying out repair and maintenance of Flange end Ball Valve:
■ Please note that even after closing the flange ball valve, there is fluid under pressure inside the valve body.
■ Release the line pressure and leave the valve in the open position before servicing the flange ball valve.
■ Disconnect the power or air supply from the driving mechanism before repairing the flange ball valve.
■ Disconnect the actuator from the bracket before maintenance.
■ Release only the upstream and downstream pipelines of the flange ball valve before disassembly.

Disassembly of Flange Ball Valve
1. Keep the valve in the half-open position to flush and remove the dangerous substances that may exist inside and outside the valve.
2. Close the flange end ball valve.
3. Remove the connecting bolts and nuts on the flanges on both sides, and then completely remove the valve from the pipeline.
4. Disassemble the drive device-actuator, connecting bracket, anti-loosening washer, valve stem nut, butterfly spring, wear plate, and valve stem packing in order.
5. Remove the body cover connecting bolts and nuts and separate the valve cover from the valve body and remove the valve cover gasket.
6. Make sure that the flange ball valve is in the “off” position. Now the valve body can be easily removed, and then remove the valve seat.
7. Push the stem lightly through the hole in the valve body until it is completely removed, and then remove the O -ring and the packing under the stem.
Note: Please be very cautious to avoid scratching the surface of the stem and the sealing part of the stuffing box of the valve body.
Assembly of Flange Ball Valve
1. Clean and inspect all the removed parts.
2. It is strongly recommended to replace the seals, valve seat and bonnet gasket with a spare part.
3. Assemble in the reverse order of disassembly.
4. Tighten the flange connection bolts crosswise with the specified torque.
5. Tighten the stem nut with the specified torque.
6. After installing the actuator, input the corresponding signal to rotate the valve core to rotate the valve stem to make the valve open and close.
7. If possible, please perform a pressure seal test and performance test on the valve according to relevant standards before reinstalling the pipeline.
8. The packing must be locked again.
9. If there is slight leakage at the packing,
– the stem nut must be locked again or
– replace the valve seat and seal.