The angle globe valve is a modification of the basic standard pattern globe valve where the ends are at an angle of 90 degrees. ZECO angle globe valves have a streamlined curved bore to create optimal flow and lower CV value. They are used in applications that have periods of pulsating flow because of their capability to handle the slugging effect of this type of flow. To avoid accumulation and crystallization of the medium, packing flushing and heating steam jackets can be added to the valve design.
What is an Angle Globe Valve?
Angle Pattern Globe Valves Design is a modification of the basic Tee Pattern Globe valve. The ends of Angle Globe Valves are at an angle of 90 degrees, and fluid flow occurs with a single 90 degrees turn. They have a slightly lower coefficient of flow than wye-pattern Globe valves.
The Role and Amount of Angle Globe Valve
The role and amount of angle valve such as DIN angle type Globe Valve in the decoration:
Angle valves, also called triangle valves, are usually used to connect water pipes and faucets to adjust the amount of water.
The role of the Angle Globe Valve:
(1) Adjust the amount of water to make the water output of the faucet more suitable for use;
(2) In case the faucet needs to be repaired, it is not necessary to cut off the main valve, as long as the corresponding angle valve is closed;
Classification of Angle Globe Valve
These valves can be classified depending on various parameters:
Design of Valve Disc: Conventional or Ball disc, Composition disc, and Plug type disc.
Disc–Stem configurations of Valve: Rotating Stem with Integral or Non-Integral Disc and Non-Rotating Stem with Integral Disc or Non-Integral Disc.
Valve Stem Screw: Inside and Outside stem screw.
Bonnet Design of Valve: Bolted Bonnet, Welded Bonnet, Flanged Bonnet, Union ring Bonnet, and Pressure seal Bonnet
How does an angle globe valve work?
The angle globe valve’s opening and closing sections are plug-shaped valve discs, the sealing surface is smooth or conical, and the flap travels linearly down the fluid’s centerline. The inlet and outlet channels of an angle globe valve, also known as an angle valve, are not in the same direction, creating a 90° right angle. This form of globe valve allows the medium flowing through it to change its flow path, resulting in a pressure drop.
Features and benefits of Angle Globe Valve
The angle globe valve has a simple design, efficient sealing, high performance, and a nice appearance. The sealing surface is made of rough steel, which is wear-resistant, corrosion-resistant, leak-proof, and has a long service life. The surface of the valve stem has been nitride and tempered. It has excellent anti-corrosion and anti-friction properties, as well as good sealing and reliability.
The angle globe valve’s most significant advantage is that it can be mounted at the corner of the piping structure, saving 90° elbows and making it simple to operate. Angle-type globe valves are ideal for use in synthetic ammonia processing systems and fertilizer plant refrigeration systems. 2500LB is very common in the ammonia synthesis process due to the high pressure needed in the grinding, synthesis, and compression parts. As a result, it is made of forged steel, has high internal and external sealing requirements, has a strong fluid force on the disc, and needs the least amount of driving force while switching. The above conditions can be met by using an angle globe valve.
Angle Globe Valve Application
Angle globe valves can be used in pipelines for the gasoline, mineral, pharmaceutical, fertilizer, electric power, recycling machinery, gas supply, cooling and freezing systems, boiler steam systems, and hot oil systems, and other industries. It can be used to break off or link the pipeline medium in various working conditions, from nominal pressures of 150LB to 2500LB and working temperatures of -40 to 500°C.
They are suitable for pipelines that do not have strict requirements for fluid resistance, i.e., pressure loss.
These valves come in a practical size limit of NPS 12 (DN 300). Valves larger than NPS 12 (DN 300) are rarely used. However, sizes up to NPS 48 (DN 1200) have been manufactured and used.
The pressure difference across the valve disc must not exceed 20 percent of the maximum upstream pressure or 200 psi (1380 kPa), whichever is less.
These valves can be considered for the equipment or pipelines with flow medium at high-temperature and high-pressure, and pipelines with steam mediums and DN<200mm.
These valves are generally installed for low temperature and low-pressure applications so that pressure is under the disk.
For high temperature and high-pressure applications, like steam, valves are installed so that pressure is above the disk.
These valves can be used for small applications as valves for instruments, sampling, pressure gauge, etc.
For highly toxic mediums, valves with bellow seals should be used.
Angle Globe Valve applications can be commonly identified in industries like shipbuilding, petrochemicals, pharmaceuticals, aerospace, etc.
They are used to control medium flow in cooling water systems, fuel oil systems, etc.
These valves are also used for Feedwater, chemical, air, lube oil, and similar services where pressure drop is not a concern.
They are deemed most appropriate for applications where leakage and safety are significant concerns, such as high point vents and low point drains.
Due to their design, these valves are widely used in the control circuits to control a wide range of flow and pressure drop.
The durability to sustain an extensive range of temperatures and pressures enables it to be used in a high-pressure environment such as steam, hydraulics, etc.
How to select an Angle Globe Valve?
There are generally full copper angle valves and alloy angle valves, and all copper has a longer service life. As for the cold water angle valve and the hot water angle valve, the blue and red signs are generally different, which is convenient for identification. The material work price is the same.
Some of the essential criteria for the selection of Angle Globe valve is
To choose as per the purposes, operating conditions, and operation control methods of the selected valves.
To choose as per the properties of the working medium, i.e., working pressure, working temperature, corrosion performance, the viscosity of the medium, whether it contains solid particles, or whether it is toxic, flammable, explosive, etc.
To choose the valve as per requirements of the fluid characteristics, i.e., flow resistance, discharge capacity, flow characteristics, and sealing level, etc.
To choose as per installation size and external size requirements, i.e., nominal diameters, connection methods, connection sizes with pipelines, external sizes, or weight limitations, etc.
To choose as per additional requirements for valve product reliability, service life, and explosion-proof performance of their electric devices.
Some Important Points in Selection Parameters
If the valves are to be used for control purposes, the following additional parameters must be determined:
- – methods of operation,
- – maximum and minimum flow rate,
- – pressure drop for regular flow and at closing,
- – maximum and a minimum pressure of valve inlets.
In addition to the basics mentioned above, understand the internal structures of various valves in detail for reasonably and correctly selecting the valves so that the preferred choice of valves can be made.
Valves are the final control in the pipelines. The opening and closing of the valve control the way of medium flow in the pipelines.
The shape of the valve flow channels gives the valve specific flow characteristics. This must be taken into account when selecting the most suitable valves for the pipeline system.
Angle Globe Valve vs Globe Valve
The basic design of this valve is the same as a globe valve, but they have a fundamental difference in the direction of fluid flow as in the angle valve, the fluid makes a 90° turn. These valves offer less resistance to flow than a globe valve with an elbow which it would replace. An angle valve reduces the number of joints in a line, in addition to saving installation time. They are also used in applications with periods of pulsating flow because of their capability to handle the slugging effect of this type of flow.
The angle pattern valve body has two benefits if the globe valve is installed around a pipe bend. First, as opposed to the standard pattern design, the angle pattern design has a significantly lower flow resistance. Second, the angle pattern decreases the number of pipe joints and eliminates the need for a pipe elbow.
Method of purchase:
We are China Industrial Valves Brand, please feel free to contact us. Be sure to satisfy you!
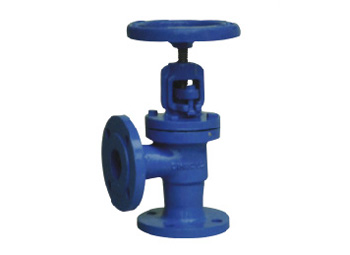
Related Tags :
Ten articles before and after
Hello world!
Gate Valve Vs Butterfly Valve Comprehensive Compare Guide
How to Measure Butterfly Valves
What is a Double Offset Butterfly Valve
How to Fix a Leaking Butterfly Valve?
China Valve Manufacturers Teach You How to Maintain The Valve
China st Gate Valve Supplier & Manufacturer
What are the basic capabilities that valve manufacturers need to have?
How to Choose A Trustworthy Valve Manufacturer?
What Are The Trends in the Development of Valve Manufacturers?