pilot valves
compressor pressure relief valve
firomatic valve
hydraulic flow regulator valve
Pinch Valves are suitable for isolating and controlling abrasive, corrosive, and fibrous materials. The pinch valve is increasingly being utilized as an isolating valve or modulating valve for powder, sludges, dust, emulsions, gaseous materials, granulates, pellets, and other similar materials.
What Is A Pinch Valve?
The pinch valve is a unique type of valve with a distinct construction that is well-known for its excellent wear and corrosion resistance and is ideal for controlling the transmission of granular slurry or chemical media in low-pressure pipes.
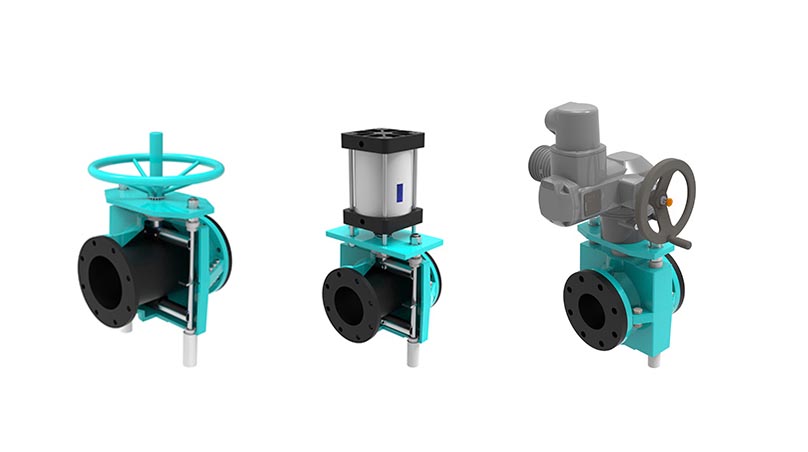
Because of the pinch valve’s outstanding corrosion resistance, wear resistance, sealing performance, and extended service life of the valve body, the sleeves of the pinch valve could be replaced on a regular basis, saving expenses and producing superior economic advantages for users.
Pinch valves can replace gate valves, ball valves, globe valves, diaphragm valves, slurry valves, and other stainless steel valves, saving costs while increasing service life by 5-10 times.
The pinch valve substitutes the stainless steel clamp and can be used to continue excellent working normally in an acid corrosion environment inside and outside. This valve is extensively used in pulp, sewage, slag, cinder, sediment, and other work conditions, and it can quickly control the flow volume and turn off the pipeline.
Based on the different drives for pinch valves, we can categorize three types of pinch valves.
- Manual-operated pinch valves
Manual-operated pinch valves are powered by a handwheel.
- Air-operated pinch valves
Air-operated pinch valves are powered by compressed air.
- Electric-operated pinch valves
Electric-operated pinch valves are powered by electric power, like 24V.DC, 220V.AC, or 380V.AC.
What Is A Pinch Valve Used For?
When solid or liquid goods comprising particles, powder, fiber, slurry, and other abrasive substances are delivered via pipelines, or when chemical procedures with corrosive media are used, the pinch valve is the ideal choice. So simply say a pinch valve is used for the transport of particles, powders, fibers, slurries, or corrosive media in the pipeline.
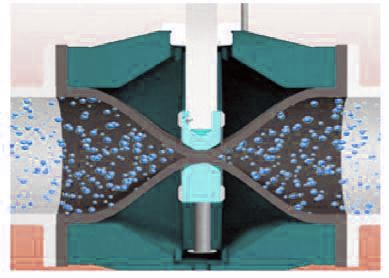
Pinch valves are commonly used in wastewater treatment plants (sludge treatment, gravel cleaning, raw sewage, lime, carbon sludge), power plants (FGD systems, ash removal systems, coal conveying), mining (tailings, flotation control, sludge discharge lines, tailings filling, various other slurries) chemical processes (corrosive and abrasive media, powders, particles) and paper mills, food industry, pulp mills, glass, electronics industry, cement industry, sand, and industrial wastewater treatment plants and many other fields.
What Are The Advantages of Pinch Valves?
Pinch valves are also referred to as squeeze valves, rubber liner valves, rubber tube valves, air sleeve valves, clamp-off valves, and so on. The inner sleeve is the most important part of the pinch valve, as it can withstand corrosion, wear, and capable pressure. The quality of the pinch valve is determined by the quality of the rubber sleeve. The inner sleeve is squeezed by a pneumatic, electric, manual or hydraulic actuator to achieve the switching/regulating function.
The Features of Pinch Valves
- Full diameter, no obstruction of the flow path
- Low flow resistance
- No blocking
- When there are residual particles, the valve can still be closed with zero leakage
- No gaps and dead zones to prevent valve operation
- Low maintenance cost
- Simple design, not affected by the harsh external environment
Pinch valve, also known as rubber sleeve valve, is widely used in smelting, mining, electric power, chemical, food, brewing, and other sectors because the inner section of the valve uses a rubber sleeve, which improves tightness, corrosion resistance, and wears resistance.
The Main Advantages of the Pinch Valves
1. Scientific Design
Low flow resistance, non-blocking, no gaps, and dead zone to prevent valve operation, even if the medium contains residual particles, the rubber sleeve still can wrap it all, and to achieve zero leakage when valve shutoff.
2. Easy to Control
You can be on-site or across a distance for automated remote control, and it can be controlled according to their individual requirements.
3. High Resistance to Wear and Corrosion
Rubber is significantly more wear-resistant than steel, iron, and other metal components, and composition adjustments can avoid the corrosion of various chemical fluids, which makes it particularly ideal for pipeline transit management of granular slurry and chemical media.
4. Excellent Sealing
When the valve is coupled to the pipeline, no extra sealing gasket is required, the valve path and the control medium space are completely isolated, ensuring that there will never be internal and external leakage.
5. Excellent Cold Resistance Performance
As the fluid medium in the flexible tube flow, fluid crystallization caused by shell frost cracking and other problems is avoided.
6. Simple Installation and Use
In the process of valve installation, The valve can be installed in both directions, so there is no confusion about the flow direction.
7. Quick Maintenance
If the sleeve of the pinch valve is discovered to be broken, the structure can enable quick sleeve replacement, simple maintenance, and simple operation.
8. Long Service Life
THINKTANK’s pinch valve has a high-quality rubber sleeve with reinforced fabric, so it can withstand any high-frequency opening and closing operation.
9. Low Costs
All sleeve types can be replaced quickly and easily with instruction and without additional tools. So it has extremely low operation and maintenance costs.
How Does Manual Pinch Valve Work?
Pinch Shutoff Valves have been shown to be the most reliable choice for bulk handling and product transporting.
A manual pinch valve is controlled by a mechanical device and a handwheel operator. The mechanism is made up of one or two clamping rods that are horizontally positioned above and below the sleeve and are directed by two rods on the sides. The handwheel mechanism then activates the mechanism, which closes and opens the valve.
How Does The Pneumatic Pinch Valve Work?
When there is no compressed air input, the cavity between the sleeve and the valve body is connected to the atmosphere, and the fluid pressure tensions the sleeve outward. Because the increased curtain cloth layer is arranged at a certain angle within the sleeve, the axial and radial pressures of the sleeve balance each other, and the length and diameter of the sleeve do not change related to fluid pressure. The sleeve deforms under air pressure and intercepts the flow when the air source enters the cavity between the sleeve and the valve body.
A differential pressure of 2-3 bar between the air supply pressure and the working pressure then the pneumatic pinch valve closed (the differential pressure value depends on the composition of the sleeve). Because of its high resilience, the pinch valve liner fully opens when the air source is interrupted and the pinch valve body is vented.
THINKTANK Pinch Valves are Useful for a Variety of Reasons
- There are no dead zones or obstructions in the valve.
- Even with solids, still has 100% tight sealing and shut off without any leakage.
- The most lightweight valve on the market.
- A body with an elliptical form consumes less air.
- Service lifetimes that are unequaled
- There are no mechanical parts which mean outstanding total cost of end-user
- Reinforced rubber sleeves for abrasive media
- Quick closing times
- Available in stock
- Simple maintenance
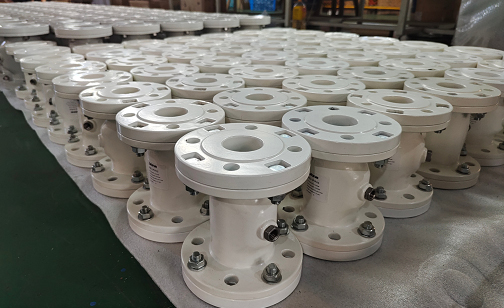
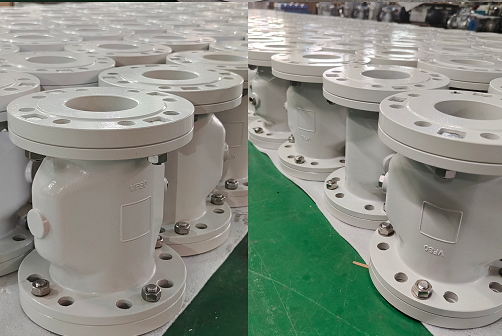
What are the Primary Factors Influencing Pinch Valve Quality?
Pinch valve is consist of four components: valve body, sleeve, opening and closing mechanism, and driving device.
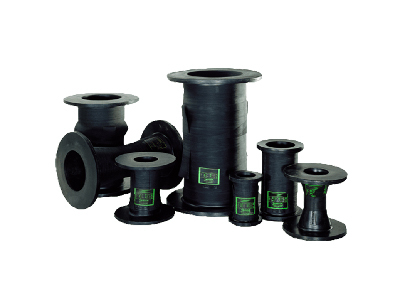
The sleeve is the key to the quality of the pinch valve, and the major variables influencing its quality are raw materials, rubber synthesis formula, processing technology, sleeve thickness, and wear-resistant anti-corrosion layer uniformity.
The following are the 5 reasons for pinch valve quality issues.
- Insufficient natural raw rubber content and excessive regenerated rubber, which cause rubber loss, significant wear & tear, and short service life.
- Incorrect rubber composition causes poor wear resistance, and acid & alkali resistance.
- The sleeve manufacturing method impacts the quality of the valve; the molded rubber sleeve wear layer is prone to uneven thickness, resulting in thin areas that are easily broken. To provide a wear-resistant layer, a pure handmade rubber sleeve is used, and the thickness of the sandwich layer is consistent. The useful life has significantly enhanced.
- Rust on the valve body, and damage to the opening and closing mechanisms, cause the valve to shut too tightly or not completely close, resulting in unsatisfactory valve usage.
- Power sources such as pneumatic and electric actuators. THINKTANK is an independent research and development manufacturer of pneumatic actuators to satisfy the torque of pinch valves with a CE certificate.
Manual Pinch Valve
Pinch valves are ideal valves for fluids containing solid particles or contaminants to isolate and regulate pipelines. Because the sleeve is the only part in touch with the medium, it is extremely resistant to wear and corrosion. Even if complicated chemical processes are occurring in the pipeline, the pinch valve is still easy to handle them. Its applications include power plants, sewage treatment plants, mining, and chemical process control.
Parts of Manual Pinch Valves
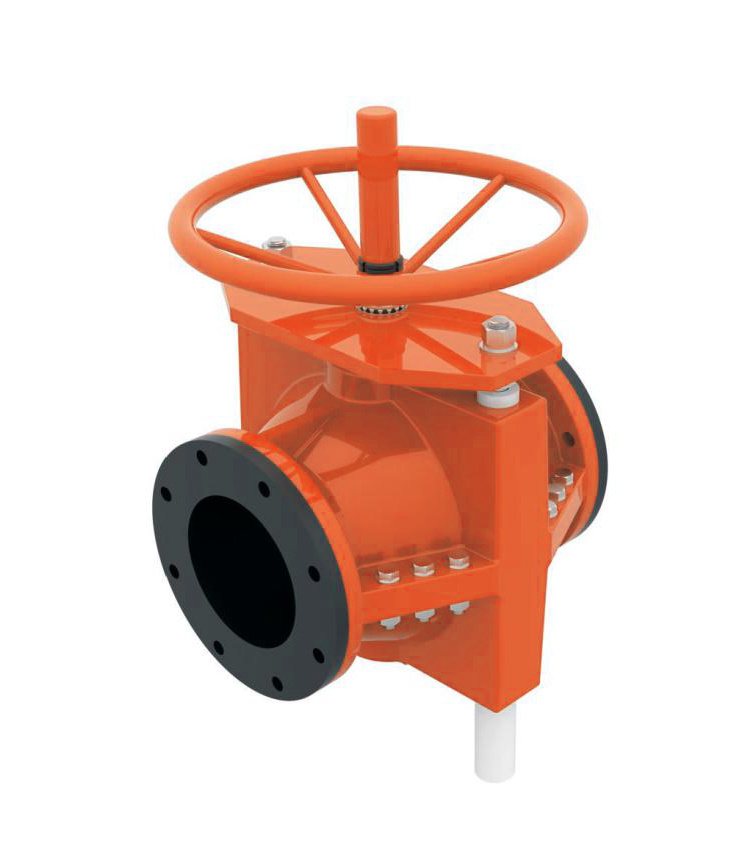
No | Part Name | No | Part Name | No | Part Name |
1 | Protective Cover | 8 | Sleeve | 15 | Bolt |
2 | Retaining Ring | 9 | Lower Body | 16 | Upper Pinch Bar |
3 | Handwheel | 10 | Nut | 17 | Side Guide |
4 | Stem | 11 | Gasket | 18 | Block |
5 | Stem Nut | 12 | Bracket | 19 | Lower Pinch Bar |
6 | Centre Bushing | 13 | Thrust Bearing | 20 | Nut |
7 | Upper Body | 14 | Upper Guide Bushing | 21 | Lower Guide Bushing |
Specifications
- Body Material: Cast Iron, Cast Steel, Aluminium
- Size: DN25 to DN1000
- Nominal Pressure: PN16
- Valve Type: Straight Through
- Max. Working Pressure: 2.5MPa
- Max. Shutoff Differential Pressure: 0.25MPa
- Full Travel Loading Time(Open to Close): ≤3S
- Effective Diameter: 25 to 1000mm
- Leakage Class: IV. (Refer to standard API598)
- Connection Type: Flange
Dimension of Pinch Valves
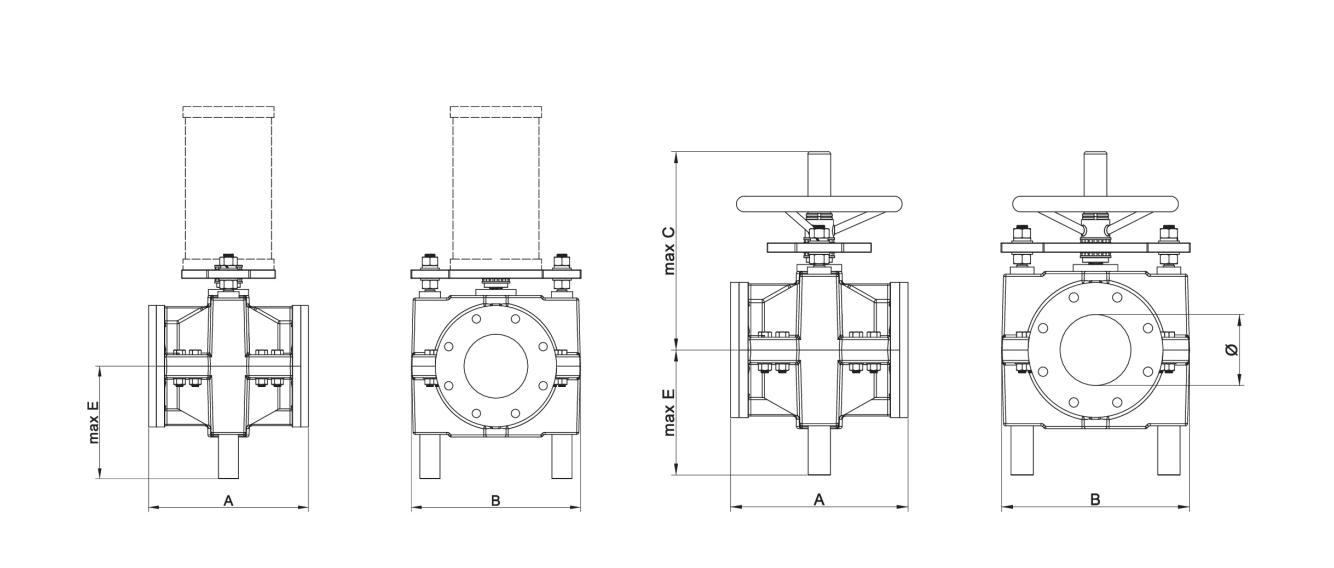
Valve Size | PN(Bar) | A | B | C | Weight/Kg (Pneumatic Pinch Valve) | Weight(Manual Pinch Valve) |
25 | 1-25 | 165 | 125 | 255 | 11 | 8 |
32 | 1-25 | 165 | 140 | 260 | 14 | 10 |
40 | 1-25 | 165 | 180 | 265 | 16 | 12 |
50 | 1-25 | 165 | 190 | 280 | 18 | 13 |
65 | 1-25 | 165 | 210 | 310 | 22 | 17 |
80 | 1-25 | 200 | 245 | 370 | 36 | 27 |
100 | 1-25 | 250 | 278 | 410 | 46 | 33 |
125 | 1-25 | 310 | 340 | 465 | 74 | 48 |
150 | 1-16 | 375 | 400 | 560 | 106 | 75 |
200 | 1-10 | 500 | 480 | 690 | 159 | 119 |
250 | 1-6 | 625 | 570 | 865 | 213 | 161 |
300 | 1 | 750 | 720 | 1020 | 279 | 212 |
Application
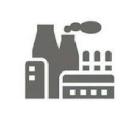
Power Plant
- FGD System
- Coal Conveying Device
- Scrubbing System
- Fly Ash Control
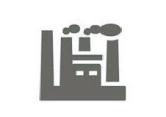
Chemical Process Control
- Corrosive and Abrasive Material
- Powder
- Particle
- Waste Treatment
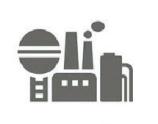
Sewage Treatment Plant
- Sludge Control
- Sand Removal
- Raw Sewage
- Lime, Carbon Slime
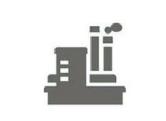
Mining Plant
- Tailing Disposal
- Flotation Control
- Multiple Mud Control
- Dredge Pipeline
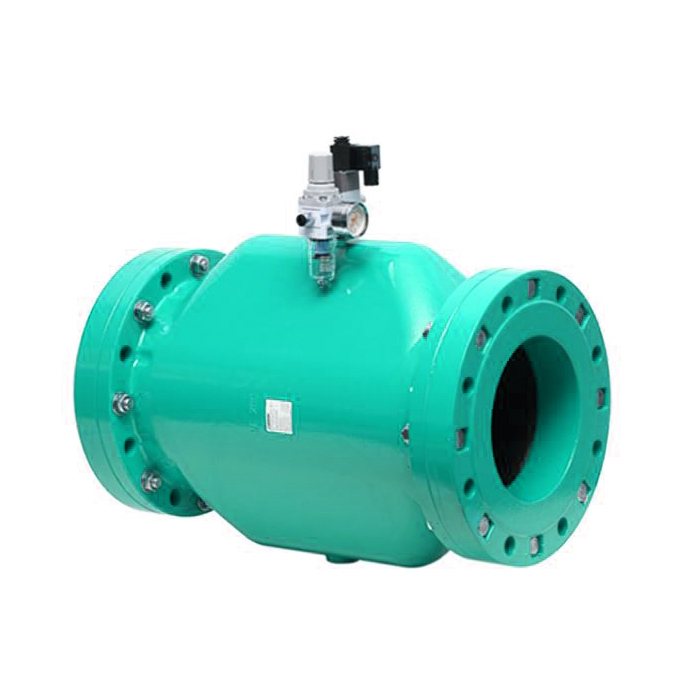
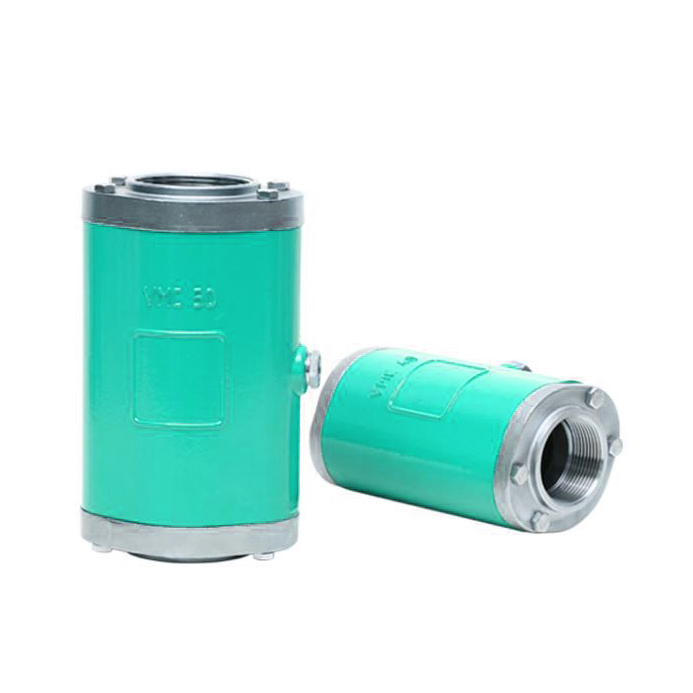

Which Benefits Will You Get If Buy Pinch Valves From THINKTANK?
● High Wear and Corrosion Resistance
Our pinch valves can handle all types of medium concentration acid and arbitrary concentration alkali salt solution, and these pinch valves can carry pulp, dry and wet powder, and crystalline material medium.
● Complete Diameter
When the pinch valve is open, its overall design may be totally integrated with the pipeline system; it won’t modify the pipe’s diameter or structure and has no impact on the pipeline’s flow medium.
● Can be Closed with Particles
Because the pinch valves are self-cleaning, any particles that accumulate in the sleeve wall are broken away when the valve is activated. This is attributed to the sleeve’s flexibility, which allows the valve to last longer than many rival products currently on the market.
● There is No Leakage.
When the valve is coupled to the pipe, the flow path and control medium space are entirely separated, and there will never be internal and external leakage, therefore eliminating running, risk, drop, leakage, and so on.
● Low Maintenance Costs
Pinch valves do not have seats, packing, rings, or telescopic tubes that need to be replaced on a regular basis. Only the sleeve needs to be replaced. The valve will be as good as new when the sleeve is changed.
Air-Operated Pinch Valve
The solution for isolating, controlling, and metering abrasive, corrosive, and fibrous goods such as granulates, powder, pellets, dust, and liquids containing solids, among others.
Sleeve Materials For Pinch Valves
Sleeve Material | Suitable Temperature | Typical Medium | Application |
SBRT Styrene Butadiene, Flowrox Blend | ‘-40°C to +110°C | Abrasive materials, diluted acid, alkali and chemical applications | Heavy wearing High cycle frequency |
EPDM Ethylene Propylene | 40°C to +120°C | Concentrated and oxidizing chemicals | Chemical applications – Applicable to 75% of all industrial chemical applications |
NBR Nitrile Rubber | -30°C to +100°C | Oils, fats, fuels, hydrocarbon, lubricants | Applications involving oils, fats and hydrocarbon |
NR Natural Rubber | ‘-50°C to +75°C | Abrasive materials, diluted acids, alkali a chemicals | High wear applications |
HNBR Hydrogenated Nitrile | -30°C to +160°C | Oils, fats, fuels hydrocarbon, lubricants | High temperature applications |
NRF Natural Rubber Foodstuff Quality White inner lining | -40°C to +75°C | Media used in food and other CIP (clean-in-place) processes, alcohol | Foodstuff applications -Fulfils FDA Food and Drug Administration) requirements |
NBRF Nitrile Rubber White inner lining | -30°C to +100°C | Vegetable and animal oils and fats | Applications involving fatty foodstuff -Fulfls FDA (Food and Drug Administration) requirements |
EPDM/B Ethylene Propylene, Blend | -40°C to +100°C | Green liquor, alkaline and extraneous matter in green liquor processes | Pulp and paper industry’s green liquor application |
CR Chloroprene Rubber | -40°C to +100°C | Chemicals, acids, several solvents, aliphatic oils, fats, lubricants | Special-purpose chemical applications -Resilient to ozone and averse weather |
FPM Fluorine Rubber (Viton⑧) | -20°C to +120°C | Chemicals, aliphatic oils, aromatic and halogenated hydrocarbon | Special-purpose chemical applications -Resilient to ozone and averse weather |
CSM Chloro-sulphone-ethylene(Hypalon@) | -40°C to +100°C | Chemicals, acids, several solvents, aliphatic oils, fats, lubricants | Special-purpose chemical applications -Resilient to ozone and averse weather |
IIR Butyl | -40°C to +100°C | Concentrated and acidic chemicals, vegetable oils | Special-purpose chemical applications -Impermeable to gas |
PU Polyurethane with PU lining | -10°C to +80°C | Abrasive materials, diluted chemicals, hydrocarbon, oils, lubricants | Abrasive media applications |
Different Flange Types of Pneumatic/Air-Operated Pinch Valves
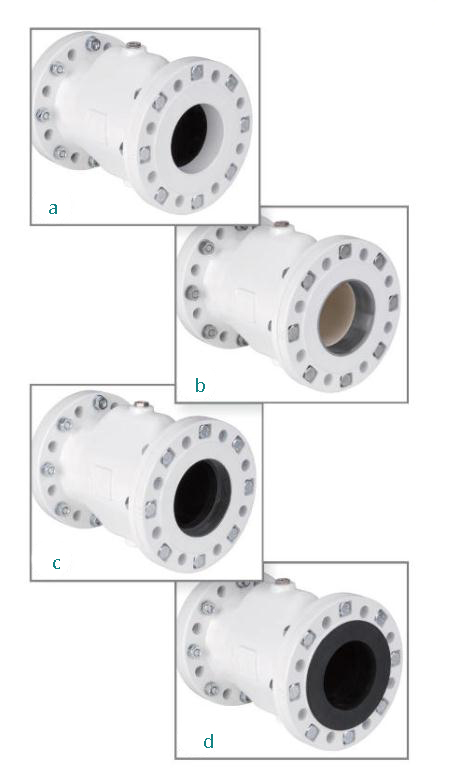
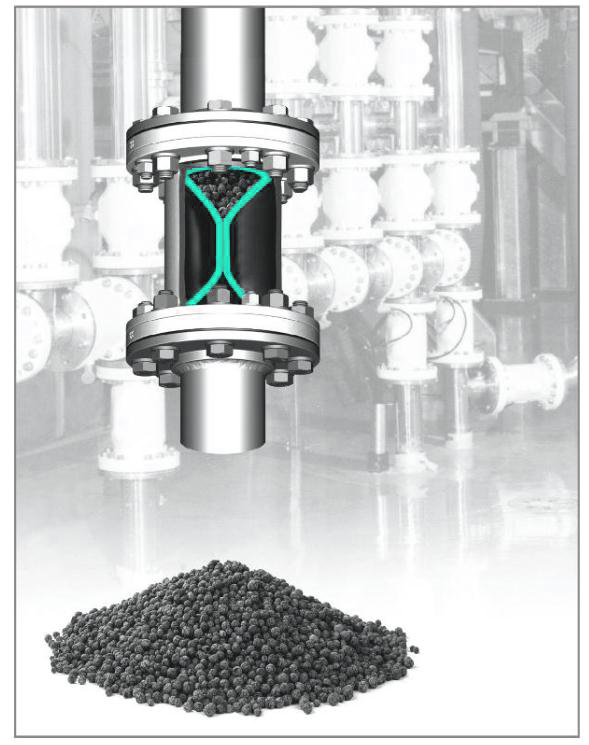
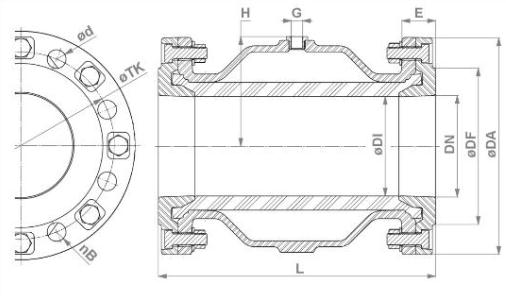
Different Flanged Ends Types
a. Aluminum Flange
b. Aluminum Flange with Stainless Stel Bushing
c. Aluminum Flange with Internal Threaded
d. Aluminum Flange with Flange Sleeve
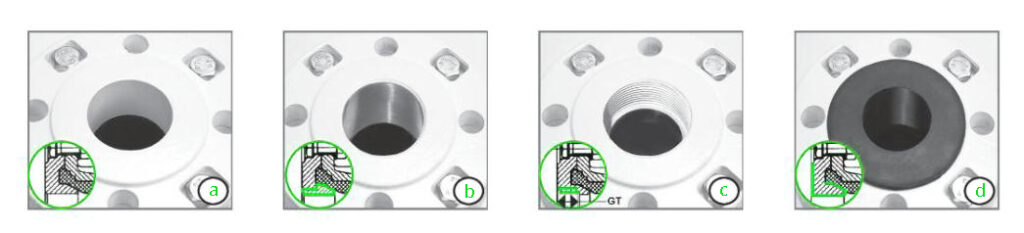
Dimensions of Flanged Ends
DN(mm) | D1 | DA | DF | nB (number of holes) | Φd | ΦTK | L | G | H | E | PS Max. (Bar) | G1 (Internal Threaded) | GT |
40 | 40 | 150 | 88 | 4 | 18 | 110 | 155 | G1/4″ | 56 | 28 | 6 | G11/2″ | 19 |
50 | 50 | 165 | 102 | 4 | 18 | 125 | 183 | G1/4″ | 65 | 28 | 6 | G2″ | 24 |
65 | 65 | 185 | 122 | 4 | 18 | 145 | 183 | G1/4″ | 81 | 30 | 6 | G21/2″ | 22 |
80 | 80 | 200 | 138 | 8 | 18 | 160 | 228 | G1/4″ | 95 | 31 | 6 | G3″ | 22 |
100 | 100 | 220 | 158 | 8 | 18 | 180 | 280 | G1/4″ | 112 | 35 | 6 | G4″ | 20 |
125 | 125 | 250 | 184 | 8 | 18 | 210 | 348 | G1/4″ | 136 | 40 | 6 | – | – |
150 | 150 | 285 | 212 | 8 | 22 | 240 | 418 | G1/4″ | 160 | 43 | 6 | – | – |
200 | 200 | 340 | 268 | 8 | 22 | 295 | 558 | G3/8″ | 206 | 60 | 4 | – | – |
250 | 250 | 395 | 320 | 12 | 22 | 350 | 680 | G1/2″ | 266 | 67 | 3 | – | – |
300 | 300 | 445 | 370 | 12 | 22 | 400 | 820 | G1/2″ | 306 | 70 | 3 | – | – |
Threaded Ends Dimension of Pneumatic/Air-Operated Pinch Valves
DN(mm) | D1 | D2 | IG | GT | L1 | L2 | G | H |
10 | 46 | 35 | G3/8″ | 12 | 68 | 80 | G1/8″ | 23 |
15 | 56 | 47 | G1/2″ | 15 | 85 | 95 | G1/8″ | 28 |
20 | 62 | 49 | G3/4″ | 17 | 93 | 103 | G1/8″ | 32 |
25 | 72 | 57 | G1″ | 20 | 110 | 120 | G1/8″ | 37 |
32 | 80 | 66 | G11/4″ | 21 | 130 | 140 | G1/4″ | 45 |
40 | 90 | 77 | G11/2″ | 21 | 150 | 160 | G1/4″ | 50 |
50 | 110 | 88 | G2″ | 25 | 175 | 185 | G1/4″ | 60 |
65 | 139 | 115 | G21/2″ | 30 | 173 | 200 | G1/4″ | 74 |
80 | 173 | 133 | G3″ | 33 | 213 | 230 | G1/4″ | 90 |
100 | 203 | 156 | G4″ | 20 | 264 | 280 | G1/4″ | 107 |
Electric-Operated Pinch Valve
The only difference between the air-operated pinch valve and the electric-operated pinch valve is the type of actuator or power that is utilized. Our pinch valves are used in applications ranging from dirty abrasive industrial slurries and powders to sanitary-grade food and pharmaceuticals.
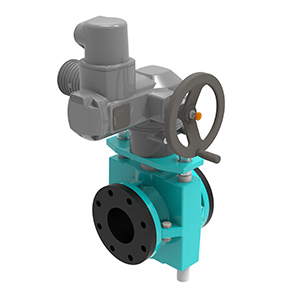
In Conclusion
Now we know the sleeve is the key point to influence the quality of pinch valves, our pinch valves are used in applications from dirty abrasive industrial slurries and powders to sanitary-grade food and pharmaceuticals with good quality. Please do not hesitate to contact us if you have any questions.
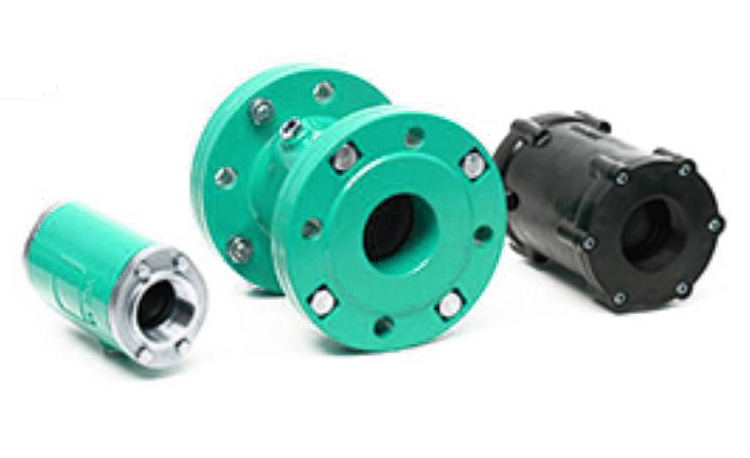
If you want to keep learn knowledge for typical application of industries, we recommend you to read the following posts.
Valves and Regulators Used for Tank Blanketing System – Tank Pressure Control
How to Select Oxygen Control Valve in Chemical and Steel Plants?
Can an industrial valve control the flow rate in the piping system? How to control it?
3 Typical Systems of Steam Pressure Reducing Station
Control Valves Are Used in The 4 Main Systems of The Power Station
2 Steps to Selecting the Right Control Valves for Your Steam Systems
How to Correctly Select a Right Safety Valve or Pressure Relief Valves/PRVs for Your System?